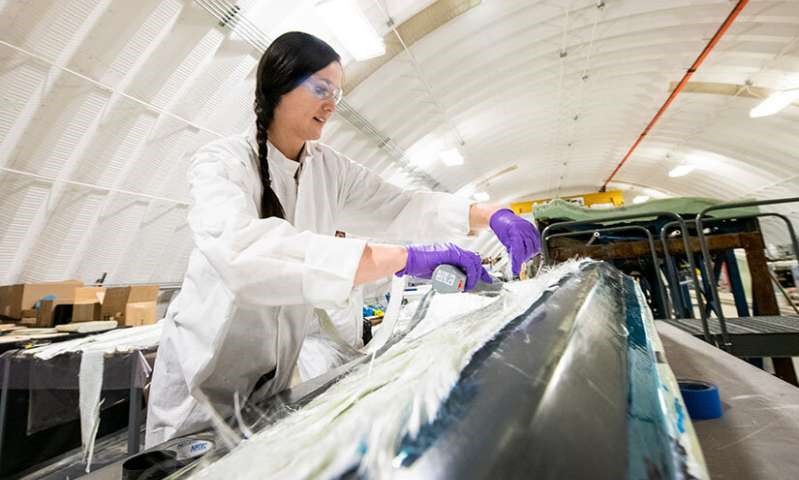
18 نوامبر 2020توسط آزمایشگاه ملی انرژی های تجدیدپذیرRobynne Murray ، محقق NREL ، روی یک تیغه توربین کامپوزیت ترموپلاستیک در مرکز آموزش و فناوری ساخت تولید کامپوزیت ها در پردیس Flatirons NREL کار می کند. اعتبار: دنیس شرودر ، NREL
یک ماده جدید برای پره های بادی که قابل بازیافت است می تواند صنعت نیروگاههای بادی را دگرگون کند و انرژی تجدیدپذیر را نسبت به گذشته پایدارتر کند و در عین حال هزینه های این فرآیند را کاهش دهد.
در این راستا استفاده از رزین ترموپلاستیک در آزمایشگاه ملی انرژی های تجدید پذیر (NREL) تأیید شده است. محققان با ساخت یک تیغه توربین بادی به طول 9 متر با استفاده از این رزین جدید ، که توسط یک شرکت در پنسیلوانیا به نام Arkema Inc ساخته شده است ، قابلیت رزین ترموپلاستیک را نشان دادند. محققان اکنون یکپارچگی ساختاری یک کامپوزیت ترموپلاستیک تیغه ای به طول 13 متر را تأیید کرده اند ، که همچنین در NREL تولید می شود.
رزین ترموپلاستیک علاوه بر جنبه بازیافت ، می تواند ساخت تیغه های طولانی تر ، سبک تر و کم هزینه را نیز امکان پذیرکند. ساخت تیغه ها با استفاده از سیستم های رزینی ترموست فعلی به انرژی و نیروی انسانی بیشتری در تأسیسات تولیدی احتیاج دارد و محصول نهایی اغلب در محل دفن زبالهانباشته می شود.
درک بری ، مهندس ارشد NREL ، گفت: “با بکار گیری سیستم های رزین گرما یی ، تقریباً مانند زمانی است که شما یک تخم مرغ را سرخ می کنید. “اما با یک سیستم رزین ترموپلاستیک ، می توانید تیغه ای از آن درست کنید. آن را تا دمای خاصی گرم می کنید و دوباره ذوب می شود. می توانید رزین مایع را پس گرفته و دوباره از آن استفاده کنید.”
بری نویسنده مقاله جدیدی با عنوان “مقایسه ساختاری تیغه توربین بادی کامپوزیت ترموپلاستیک و تیغه توربین بادی کامپوزیت ترموست” است که در مجله انرژی های تجدید پذیر منتشر می شود.
NREL همچنین یک مدل فنی-اقتصادی برای کشف مزایای استفاده از رزین ترموپلاستیک در پره ها ایجاد کرده است. تیغه های توربین بادی فعلی در درجه اول از مواد کامپوزیتی مانند فایبرگلاس که با رزین ترموست تزریق می شوند ، ساخته می شوند. با یک رزین ترموست اپوکسی ، فرایند تولید نیاز به استفاده از گرمای اضافی برای عمل آوری رزین دارد که به هزینه و زمان چرخه تیغه ها می افزاید. رزین ترموپلاستیک در دمای اتاق انجام می شود. این فرایند به نیروی کار زیادی احتیاج ندارد که حدود 40٪ هزینه یک تیغه را تشکیل می دهد. در فرایند جدید ، محققان تشخیص دادند ، می تواند ساخت تیغه ها را حدود 5 درصد ارزان تر کند.
NREL محل استقرار آموزش ساخت و تولید کامپوزیت ها (CoMET) در پردیس Flatirons در نزدیکی بولدر ، کلرادو است. در آنجا ، محققان پره های توربین کامپوزیتی را طراحی ، ساخت و آزمایش می کنند.
موری گفت: “مواد ترموپلاستیک انرژی بیشتری را از بارهای پره های ناشی از باد جذب می کند ، که می تواند باعث کاهش فرسودگی وریزش این بارها به بقیه سیستم توربین شود ، که این یک چیز خوب است.”
با بزرگ شدن سایزهای تیغه ها ، مشکل نحوه حمل آنها از یک مرکز تولید نیز افزایش می یابد. اما رزین ترموپلاستیک همچنین می تواند به تولیدکنندگان امکان ساخت تیغه در محل را بدهد ، و این مسئله مشکلی را که صنعت با آن رو به رو می شود به سمت تیغه های بزرگتر و بلندتر کاهش می دهد.