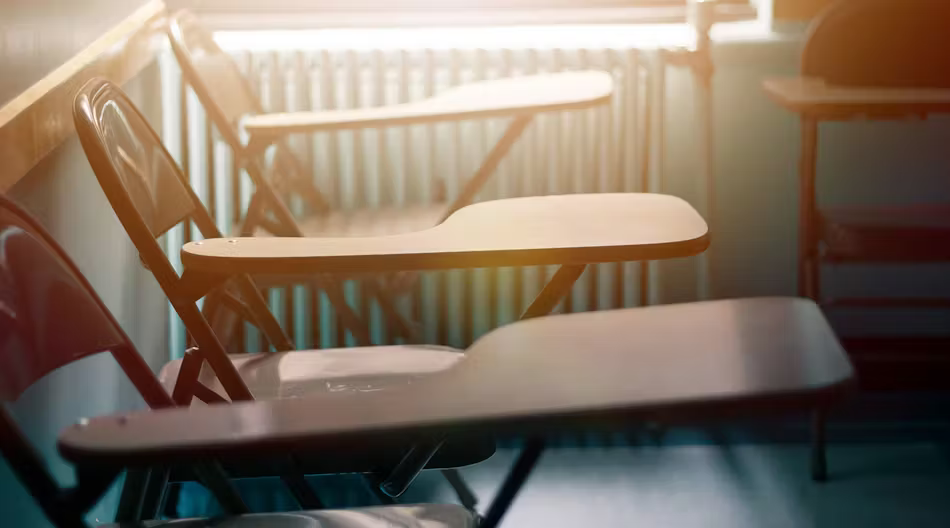
28 فوریه 2018-لری فست
سوال: بسیاری از پیشرفت های مستمر و کتاب های ناب/ مردم می گویند شما همانقدر از شکست یاد می گیرید که از موفقیت. شما مدت زیادی در این صنعت بوده اید. آیا می توانید مثال خوبی از اینکه چگونه یک شکست (یا شکست) به یک تجربه یادگیری برای شما یا تیمتان تبدیل شده است، بیاورید؟
پاسخ: چه سوال خوبی. البته مثال های خاص زیادی وجود دارد که می توانم ذکر کنم. یادگیری بسیار زیادی وجود دارد که به طور طبیعی در تمام مسیرهای سفر CI رخ می دهد. اما دو موقعیت فرهنگی عمده در حرفه من وجود دارد. چرا؟ زیرا آنها طرز فکری را شکل دادند که با پیشرفت شغلی من در سمتهای رهبری اجرایی، در بهبود مستمر از آن استفاده خواهم کرد.
اولین درس مهمی که در سالهای اولیه آموختم این بود که رهبران اغلب خوب گوش نمیدهند و در نتیجه فرصتها را برای مشارکت دادن دیگران در حل مشکلات روز از دست میدهند. به نظر میرسد این انتظار در فرهنگ وجود دارد که رهبران برای حل هر مشکلی به اندازه کافی باهوش باشند و افرادشان در طول سالها «آموزش دادهاند» تا به آنها اطاعت کنند. (البته، هیچ کس در آن زمان به اندازه امروز آنقدر باهوش نبود.) با این حال، به دلیل آن الگو، مشاهده کردم که رهبران تمایل داشتند وظایف خود را یک یا چند سطح پایین تر از آنچه که برای انجام آن دستمزد دریافت می کردند، انجام دهند. یکی از مخرب ترین پیامدهای این رفتار، سرزنش بازی بود که در جریان تعاملات بین ناظران خط اول، مهندسان، بازرسان کیفیت، توزیع کنندگان رخ داد. تقریباً برای هر اختلالی که در مغازه رخ می داد، اپراتورهای دستگاه بیشتر تقصیر را بر عهده گرفتند.
پارادایم ساده بود: اپراتورها هر روز اشتباهات زیادی مرتکب می شوند. شواهد واضح بود: نرخ قراضه بالا. کارهای عقب افتاده عظیم و بی پایان. هزینه های غیرمستقیم بسیار بالایی که با تعمیر یا اسقاط مواد همراه است. یکی دیگر از عوامل اصلی این بود که استفاده ضعیف از ماشین باعث هزینههای بالاتر و تاخیر در تحویل و زمانبندی مجدد میشد. موجودیهای در حین فرآیند بهطور فوقالعادهای بالا بود و موادی که در کف کارگاه گیر کرده بودند. موجودی کالاهای تمام شده بیش از حد بود. موجودیهای بافر برای به حداقل رساندن تأثیر بر وعدههای تحویل مشتری، حفاظتی ایجاد کردند. با وجود این هدر رفت پول نقد، محموله های به موقع در دهه 80 فرو رفت.
ناظران و مدیران بخش هر روز صبح برای بررسی تمام ضایعات گرد هم می آمدند. داده های کمی درگیر بود. فقط انبوهی از ضایعات با برچسبهایی روی هر نوع ماده تا بتوان ضایعات را بهدرستی هزینه کرد و گزارش کرد. سؤالات شرکت کنندگان در جلسه به ندرت مبنای واقعی داشت، بلکه بیانگر نظرات ناظران، مهندسان و بازرسان بود. اپراتورها هرگز در این بررسی ها شرکت نکردند. فقدان داده های خوب مانع از هرگونه درک علت اصلی می شد. این نظرات همان مردم هر روز صبح بر اساس «دانش» تجربی بود. این جلسات تقریباً همیشه یک اتلاف وقت بود. در اینجا به سادگی از هیچ فرآیند خوبی برای ریشهیابی و حل مشکلات استفاده نمیشود. این یک دایره بی فکر و بی پایان از سرخوردگی بود.
چیز خوبی که از این تجربیات حاصل شد این بود که خدمت در نقشهای رهبری مستقیم تولید، تعامل مستقیم بیشتر با افراد ساعتی در چهار بخش، یک فرصت یادگیری عالی بود. من همچنین راحتتر غواصی عمیقتری در مسائل مربوط به کف مغازه داشتم و به دنبال اطلاعات اپراتور بودم. من با اپراتورها ارتباط برقرار کردم. من دیگر فقط ورودی های مدیریت را نمی شنیدم. اگر مشکلی بود که ارزش دخالت مدیریت را داشت، دریافت ورودی اپراتور بخشی از فرآیند می شد. با گذشت زمان، برای رهبران سطوح پایینتر طبیعیتر شد که ابتدا به دنبال ورودی اپراتور باشند، نه آخرین. نتیجه این بود که اپراتورهای ساعتی ماشین مشکلی ندارند.
بهجای طولانیتر کردن یک داستان کوتاه، کافی است بگوییم که من تا آخر عمرم با طرز فکر زیر ارتباط برقرار کردم و رفتار کردم.
اکثر مشکلات موجود در طبقه مغازه از جای دیگری به آنجا ارسال می شود. به احتمال زیاد آنها توسط یک فرد حقوق بگیر در یک اداره یا شاید از یک فرد غیرمستقیم ساعتی در یک نقش پشتیبانی به آنجا فرستاده شده اند.
در اینجا چند مثال رایج وجود دارد: فرآیند اطلاعیه تغییر مهندسی (ECN) بسیار ضعیف بود. اغلب دستورالعملهای تنظیم کار بهموقع بهروزرسانی نمیشدند. حسابداری همیشه تغییرات هزینه را دریافت نمی کند. کنترل تولید تغییر نرخ نمی کرد. مواد خام با کیفیت پایین از طریق فرآیند ضعیفی در دریافت بازرسی گذر کرده بود که باعث ضایعات بیش از حد و/یا سرعت اجرای آهسته تر شد. قطعات به دلیل فرآیندهای تعمیر و نگهداری ابزار ضعیف، بزرگتر شدند. تأمینکنندگان جدید مواد خام، مواد خود را در آزمایشهای آزمایشی قبل از اجرای برنامههای تولید ثابت همچنین، اطلاعات برنامه اشتباه، سفارشی نکردند.
سفارشات اشتباه وارد شدند، و سایر مسائل مربوط به فرآیند ثبت سفارش نامناسب، و همچنین فروش سفارشهایی که بدون هزینههای بسیار بالاتر از هزینهای که در حسابداری تعیین شده بود، قابل ساخت نبودند. و غیره و غیره
و همه اینها تأثیر مستقیمی بر بزرگترین مشتریان داخلی این گروه های پشتیبانی داشت: اپراتورهای ماشینی که ارزش محصول شرکت در آنها ایجاد می شود.
نتیجه گیری: افراد حقوق بگیر سطح پایین و ساعتی غیرمستقیم نیز مشکلی ندارند. رهبران ناکارآمد و فرآیندهای ناکارآمد هستند. پس چه چیز دیگری یاد گرفتیم؟
علاوه بر تجزیه و تحلیل مسئله و روشهای اقدام اصلاحی، تغییر فرهنگ برای تنظیم چارچوبی برای حفظ CI ضروری است. در اینجا نحوه ایجاد تغییر در روایت آمده است.
از نظر فرهنگی، رهبران باید انتظارات خود را بالا ببرند. مشکلات فرآیند همچنان ادامه دارد زیرا مردم آنقدر درگیر روال روزمره مدیریت بحران میشوند که دیگر فکر نمیکنند و روز را با استفاده از آدامس، بانداژ و سیم عدلبندی برای انجام موقت یک راهحل برای یک فرآیند بد تلف میکنند.
تغییر مثبت تنها زمانی آغاز می شود که هر رهبر بایستد و بگوید بس است! کاری کنید که افرادتان هر روز با فرآیندهای ناکارآمد کنار بیایند. وظیفه ما آموزش افرادمان برای نقشه برداری از فرآیندهای شکسته، یافتن موارد قطع و حل مشکلات است! حلقه بسته، فرآیندهای یکپارچه راه حل هستند. این چیزی است که کارمندان حقوق بگیر باید از روز اول یاد بگیرند که بفهمند. اما، متأسفانه، اکثر مدیرانی که من میشناختم به طور غریزی چنین فکر و عمل نمیکنند، بنابراین این اختلال بسیار ناامید کننده ادامه دارد.
من قویاً معتقدم که اپراتورها معمولاً هر روز با آمادگی برای انجام کارهای خود به خوبی سر کار می آیند و امیدوارند که روز خوبی داشته باشند. اکثر افراد حقوق بگیر و غیرمستقیم به همین امید امیدوارند. چیزی که معمولاً ریشه هرج و مرج ناشی از آن است، به فرآیندهای ضعیفی اشاره دارد که تقریباً داشتن یک روز خوب را برای کسی غیرممکن می کند.
رهبران باید طوری آموزش ببینند که راه درستی بیندیشند و تیمهایشان را برای استفاده از نقشههای جریان فرآیند/ارزش، معیارهای دقیق و سایر فرآیندهای حل مسئله، نه نظرات، آموزش دهند تا واقعاً مشکلات را با بهبود فرآیندها حل کنند. همانطور که دمینگ گفت: «ما به خدا اعتماد داریم. بقیه داده ها را می آورند.» (با احترام “و روند خوب” را اضافه می کنم.) چالشی که ما با همکاران ساعتی حقوق بگیر و غیرمستقیم خود استفاده کردیم این بود: کار ما حذف همه دلایلی است که اپراتورها روز بدی دارند.
دومین درسی که من به سختی یاد گرفتم این است که سفرهای CI بدون متعهد شدن مدیران هیئت مدیره و C-suite به رهبری این سفر طولانی شغلی و بهبود مستمر نمی تواند ادامه یابد. این بدان معنی است که اطمینان حاصل کنید که فرهنگ و انتظارات برای CI از طریق تغییرات رهبری، فروپاشی بازار و هر مانع دیگری که خود را نشان می دهد غالب می شود.
اولین تجربه من کاملا از پایین به بالا بود. پس از ترک من، در طول سالها تغییرات زیادی در رهبری وجود داشت که شامل چندین مدیر عامل، معاونان تولید، مدیران کارخانه و غیره میشد. در کمتر از 10 سال، کارخانهای که من میتوانستم به عنوان یکی از بهترینهای دنیا راهاندازی کنم، در آنجا بود. به هم ریخته و در نهایت پس از یک دهه افول دیگر بسته شد.
در شرکت دومم، جنرال کابل، من یک مدیر عامل قوی داشتم که از ابتکار CI که من بار دیگر از پایین به بالا شروع کرده بودم، حمایت کرد. عملکرد کسب و کار در ابتدا بسیار ضعیف بود، بنابراین برداشت میوه های کم آویزان نسبتاً آسان بود و بهبود قابل توجهی را در قیمت پایین و کمک های نقدی نشان داد. اما به نقطه ای رسیدیم که فرهنگ باید تغییر می کرد. این شرکت مجموعه ای از شرکت های سیم بود که از طریق اکتساب به آن اضافه شده بود و هر فرهنگ متفاوت بود. این تفاوت ها هنگام پیاده روی در تورهای گیاهی و تعامل با مدیریت محلی و کارکنان ساعتی قابل لمس بود. واضح است که ما نیاز داشتیم که یک چهره را در تولید قرار دهیم تا تفکر، فرآیندها و معیارها برای بهبود بلندمدت شرکت استاندارد شوند. تجهیزات بسیار شبیه بودند، اما فرآیندها و کار استاندارد بسیار بسیار متفاوت بود.
آزمون بزرگ در طول جلسه تیم رهبری آمریکای شمالی (LT) چند سال پس از راه اندازی ابتکار عمل CI در عملیات انجام شد. بر اساس نتایج، یکی از همتایان این سوال را مطرح کرد که آیا ما باید تغییر فرهنگ را برای شرکت خود در نظر بگیریم که همه افراد را در لیست حقوق و دستمزد مشارکت دهد. مدیر عامل با عصبانیت پاسخ داد: “ما قرار نیست فرهنگ اینجا را تغییر دهیم.” وقتی من صحبت کردم و گفتم: “خب، ما فرهنگ تولید را تغییر می دهیم!” به افتخار مدیران عامل او آرام شد، من اخراج نشدم و به نظرات جلسه LT فکر کرد و بلافاصله پس از آن به صدای بسیار قوی و حامی CI و تغییر فرهنگ لازم تبدیل شد و در عین حال ما را در عملیات تشویق می کرد که مسیر رهبری را رهبری کنیم.
بعداً وقتی آن مدیرعامل بازنشسته شد، مدیرعامل جدید که مدت زیادی در شرکت بود، قدرت، تعهد، پشتیبانی و تداوم را فراهم کرد. او هیئت مدیره را هدایت کرد تا CI را به یک استراتژی جهانی تبدیل کند. او همچنین تصریح کرد که همه عملکردها، نه فقط عملیات، بلکه باید کاملاً حامی و فعالانه درگیر بهبود فرآیندها در کارکردها و مشاغل خود باشند. این فرهنگ تا زمان بازنشستگی او چند سال پیش بود.
من از راه دور، تغییرات بنیادی را در آن شرکت طی دو تا سه سال گذشته در رأس سازمان مشاهده کرده ام و از تأثیرات شگرفی که از نظر فرهنگی منتج شده است آگاه هستم. من امیدوارم که تغییرات در بالا، همراه با فروش معلق شرکت، سفر CI را در سال 2018 که نوزدهمین سال آن خواهد بود، از مسیر خارج نکند. تقریباً نیمی از ابتکارات CI خارج از ریل هستند، کمتر از پنج مورد است. سال و کمتر از 5 درصد از سفرهای CI بیش از 10 سال طول می کشد. من تعجب میکنم. آیا فرهنگ آنقدر عمیق است که سفر آنها بتواند زنده بماند؟
این آموختن از تجربه من و از آمار، آن را تا حد ممکن واضح می کند. عدم وجود هیئت مدیره و تداوم سطح C، حمایت قوی و مشارکت فعال آنها به عنوان رهبران شرکت، CI پایدار نخواهد بود. این آزمونی است که بسیاری از شرکت ها در طول 30 سال گذشته با آن روبرو بوده اند و شکست خورده اند. نتیجه در این مورد چه خواهد بود؟
لری فست موسس و رئیس Pathways to Manufacturing Excellence و 35 سال سابقه کار در صنعت سیم و کابل است. او نویسنده 12 اصل تعالی تولید، راهنمای رهبر ناب برای دستیابی به تعالی و پایداری، دوم است.